
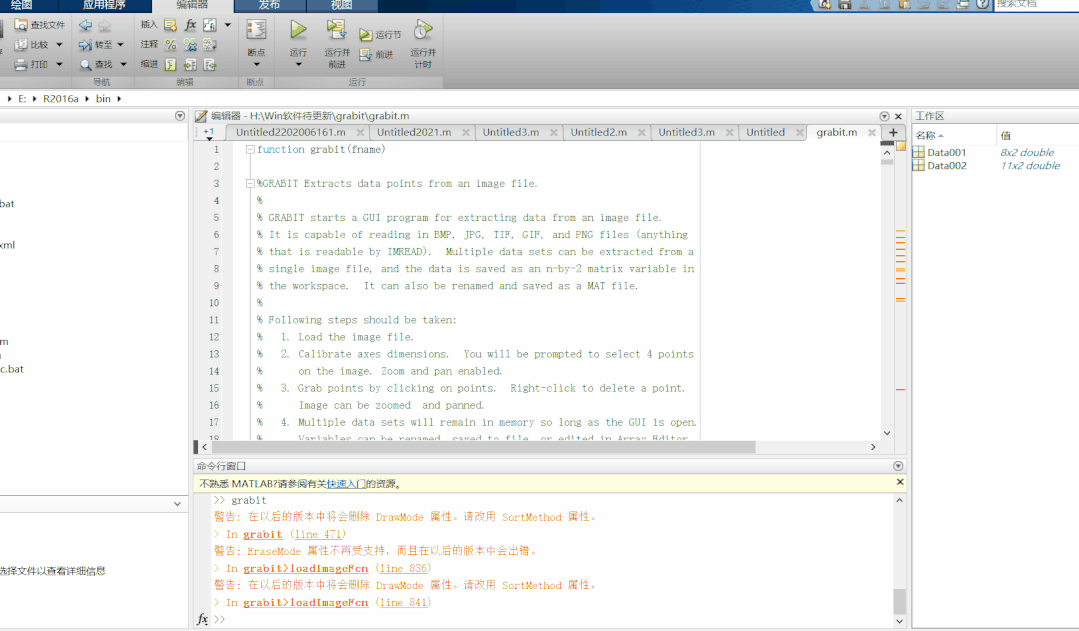
This is by no means a comprehensive course, it is simply an introduction to Matlab from the perspective of an oceanographer who uses it often. Many of the materials I used were adapted from Andrew Pershing's material, "Introduction to Applied Scientific Computing & Visualization with MATLAB", which you can find here. In January 2011 I ran a four hour workshop on using Matlab. The specimen was then cleaned with alcohol and the micro structure was studied under Olympus BX60M.James J. The specimen was etched for 13- 15 seconds in the etchant and then run under a thin stream of water. 30 Etchant which is a NH4OH based solution was used for etching copper. Polishing was done with a water based diamond suspension of 1m for 10 mins.Ī finely polished, reflective surface was obtained upon surface treatment. Ultra3000H-32) was used for cold mounting.įor the surface finishing of the prepared specimens, grinding was performed on 240 grit SiC foil for two mins, 500 grit SiC foil for 2 mins and on 1200 grit SiC foil for 6 mins.

Ultra-3000R-128)and Ultrathin 2 Hardener(Cat.

Pace Technologies Ultrathin 2 Low Viscosity Resin (Cat. The effect of the elongation in grain structure on the burr formation is studied.įor the study of the micro-structure of the raw material, annealed material and elongated material (10%,25%, 32%) a disc and a piece along the axis was cut of out of the rod for the cross-sectional view and the axial view respectively.Īs Copper C101 has a recrystallization temperature below 150C, the cold mounting technique was used for the preparation of specimens for study of the micro-structure. An elongation in grain structure is expected upon work hardening the material. When the material is strain hardened in one direction, it causes a significant change in the micro structure of the material. This strengthening occurs due to movements in dislocations and generation of dislocations. Strain hardening also known as work hardening is strengthening of material obtained by plastic deformation. This was achieved by heat treatment and strain hardening of the material in one direction. In this study, we have tried to minimize the burr formation by altering the micro-structure of the material. It is now well established that burr formation is affected by the mechanical properties of the material and the cutting conditions. In spite of all the advancements in this field, there are many challenges in minimizing the burr formation. Several studies have been conducted to reduce the burr by varying different cutting parameters or the tool geometry. Milling results in the formation of burr which has been defined as the undesirable projections formed on the edge of the material due to plastic deformation during machining. Most of the times in Precision manufacturing a material has to undergo machining where, milling is one of the most commonly used machining processes whether it involves making the mounting plates, jigs, and fixture, etc. Burr formation results in a decrease in the surface finish of the material, and it also leads to the dimensional inaccuracy of the component.

There is a strong demand for production of these high precision parts at minimal cost possible.īurr can be defined as the undesirable projections formed on the edge of the material due to plastic deformation during machining. The aim is to produce highly engineered, precision products that typically components of other industries like the automotive, aerospace, electronics, etc. Precision Machining is one of the fastest growing industries in the present day.
